Lasers for Medical Device Manufacturing
Lasers for medical device manufacturing (MDM) have come a long way in recent years, unlocking new innovations in the medical industry. Their non-contact, abrasion-resistant applications are perfect for all types of medical grade materials. Mark UDI codes or weld clear plastics and medical tubing, lasers are the ideal choice.
- Mark, cut, drill or weld medical plastics
- “Cold marking” using ultrafast lasers
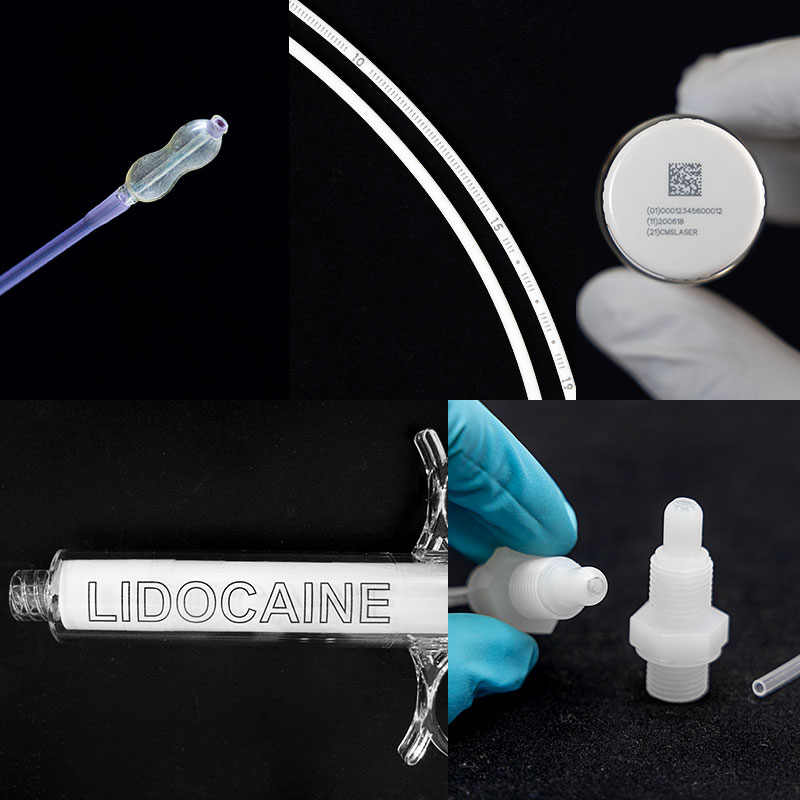
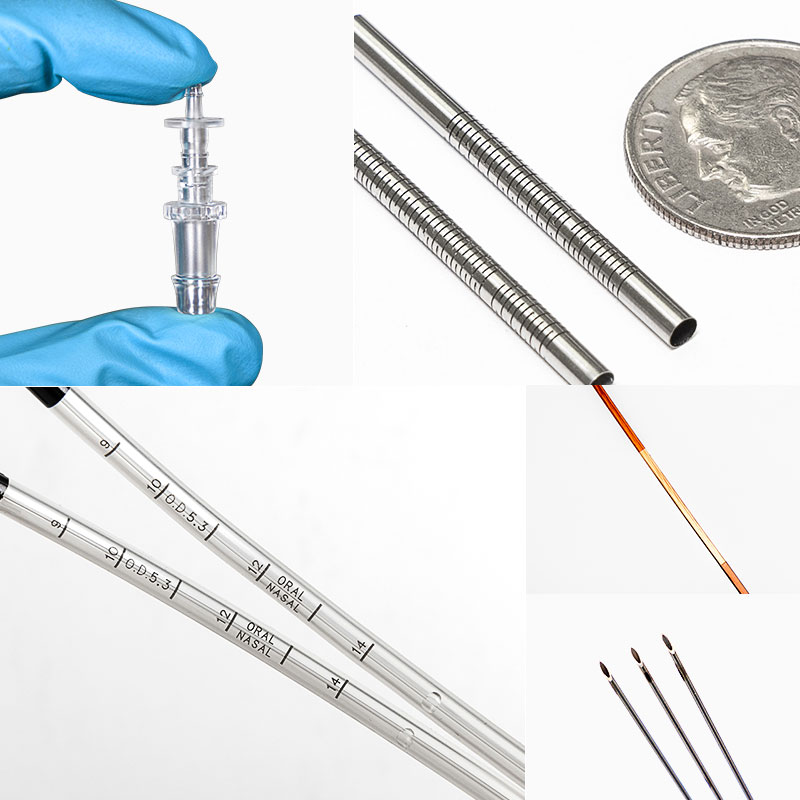
Laser Marking, Cutting, Drilling, and Welding for MDMs
Lasers are widely used in the medical device industry for various applications. In marking, lasers create permanent and precise identification codes on medical devices. Laser cutting allows for accurate shaping and fabrication of components, while laser drilling enables the creation of small, precise holes in devices. Laser welding joins different components together, ensuring strong and durable bonds.
The advantages of laser processes include high precision, minimal heat impact, reduced contamination risk, and compatibility with various materials. Laser technology enables the production of clean, accurate, and reliable medical devices. From marking unique identifiers to shaping components and creating intricate patterns, lasers play a crucial role in manufacturing medical devices with precision and efficiency.
Laser-Based Applications for Medical Device Manufacturing
From marking catheters to drilling micro holes in plastics and metals
Laser Marking Medical Devices
Laser marking offers several advantages, including high precision, durability, and the ability to mark on a wide range of materials used in medical devices.
Cold Marking with UV Lasers
The utilization of ultraviolet (UV) lasers for marking medical-grade plastics represents a ‘cold marking’ technology, leveraging photochemical interactions instead of thermal effects. This advanced process generates high-contrast, permanent marks within the plastic material itself, as opposed to creating surface oxidation. This attribute is crucial in ensuring that the markings remain bacteria-free, as they do not create areas that can trap or harbor bacterial growth.
Laser Marking UDI Information
The Unique Device Identifier (UDI) is a standard in the medical device industry that mandates Medical Device Manufacturers (MDMs) to label and track their products using GS1 standards once they are manufactured. These UDI markings must meet specific criteria, such as being permanent, high-contrast, and resistant to chemical cleaning agents.
At CMS Laser, our skilled engineers are well-versed in these standards and are dedicated to helping you develop impeccable markings. We understand the importance of creating marks that are abrasion-resistant, free from oxide formation, and safe for use in implantable devices and surgical tools. With our expertise, we ensure that your products comply with UDI requirements while maintaining optimal performance and longevity.
Laser Cutting Medical Devices
Laser cutting offers many advantages compared to other MDM cutting methods. A non-contact process, laser cutting doesn’t require blades or tools, which need to be sharpened and replaced, and doesn’t impart unnecessary force on the product. It also enables quick changeovers between cutting paths; simply select a new software file.
Application examples include cutting eyes into catheters, as well as modifying needles and cannulas.
Laser Drilling Medical Devices
Laser drilling machines provide exceptional precision, control, and non-contact processing, making them suitable for creating small holes in delicate medical components and devices. Some of the medical devices and components that utilize laser drilling machines include:
- Catheters – Laser drilling is often employed to create precise holes in catheters, which are flexible tubes used for various medical procedures such as fluid drainage, tissue sampling, or drug delivery.
-
Stents: Laser drilling helps in creating precise patterns of holes in the stent material to promote better drug delivery or enhance tissue integration.
-
Microfluidic devices: Laser drilling is essential for creating microchannels and through-holes in microfluidic devices used for medical diagnostics and lab-on-a-chip applications.
- Surgical instruments: Laser-drilled holes are also utilized in surgical instruments, such as endoscopes and laparoscopic tools.
-
Dental implants: Laser drilling is utilized in the fabrication of dental implants to create holes for inserting screws or posts that anchor the artificial teeth to the jawbone.
Laser Welding Medical Devices
There are many advantages to laser welding plastics and metals used in the medical device industry. Lasers provide exceptional precision to create immaculate, long-lasting, and hermetically sealed welds.
Utilizing focused beams that concentrate on small spot sizes, laser welding achieves thin weld line widths. Depending on the application, gantry motion or galvanometer steering can be employed to precisely direct the beam’s placement. As a result, the resulting welds are robust, durable, and impermeable, especially when combined with purpose-built fixtures. Moreover, laser welding seamlessly joins transparent plastic parts without the need for additives or causing color changes. Unlike ultrasonic welding, laser welding of plastic medical devices produces no debris.
- Laser weld clear-to-clear plastics, opaque to clear, and even metal to plastics
Laser Treating Surfaces
Laser surface treatment involves the use of high-energy laser beams to modify the surface properties of a material without physically altering its bulk properties. This technique is commonly used in the medical device industry to enhance the functionality, biocompatibility, and performance of various medical devices.
There are several ways lasers can be utilized for surface treatment:
- Laser Cleaning: High-intensity laser beams can remove contaminants, such as oils, grease, and particles, from the surface of a medical device. This ensures cleanliness and prepares the surface for further treatment or coating.
- Laser Texturing: By controlling the laser parameters, surface textures can be created on medical devices. Laser texturing can improve the friction properties, cell adhesion, or hydrophilicity of a surface, depending on the desired application.
- Laser Surface Modification: Laser beams can be used to modify the surface chemistry of medical devices, such as inducing chemical reactions or altering the composition. This can enhance biocompatibility, corrosion resistance, or other specific properties.
- Laser Surface Hardening: Certain laser techniques can selectively heat the surface of a medical device, causing localized hardening of the material. This is often used to increase the wear resistance and durability of components.
Laser Wire Stripping Magnet Wires
Magnet wires, also known as winding wires or enameled wires, are insulated copper or aluminum wires used in the construction of electromagnetic devices such as transformers, motors, and solenoids. These wires have a thin insulation coating, usually made of enamel, which allows them to be wound into coils or used in intricate electrical components.
CMS Laser has developed a laser wire stripping solution designed to remove the coatings on magnet wires.
Related Videos
View MoreOur Experience with Medical Device Manufacturing
With over 40 years of business, our team has the expertise to develop solutions for MDMs
Cold Marking With UV Lasers For Plastic Medical Devices
Achieve non-thermal, UDI compliant laser marking of medical device plastics using an ultraviolet laser.
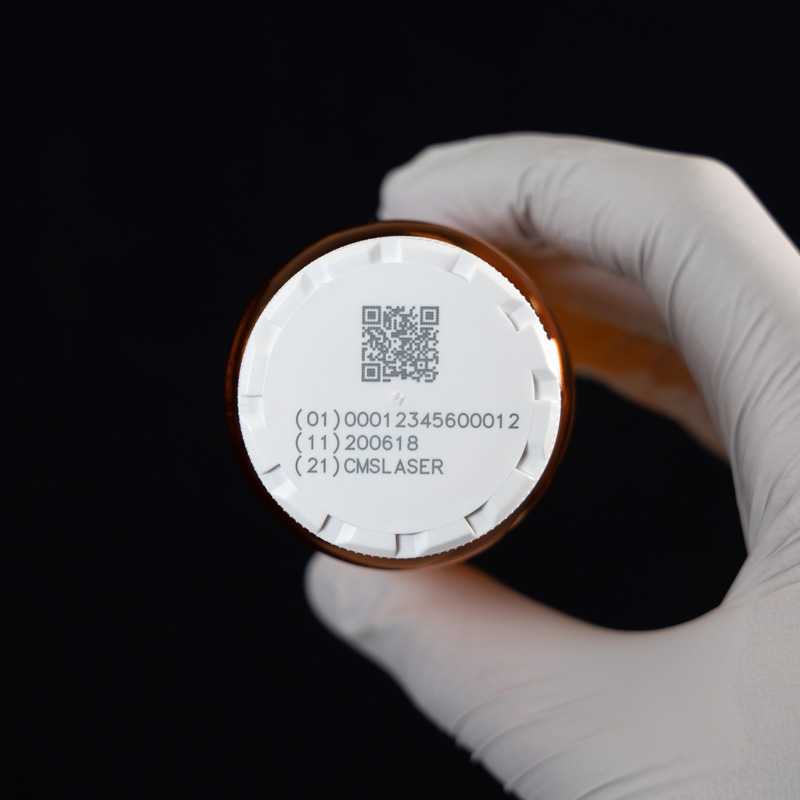
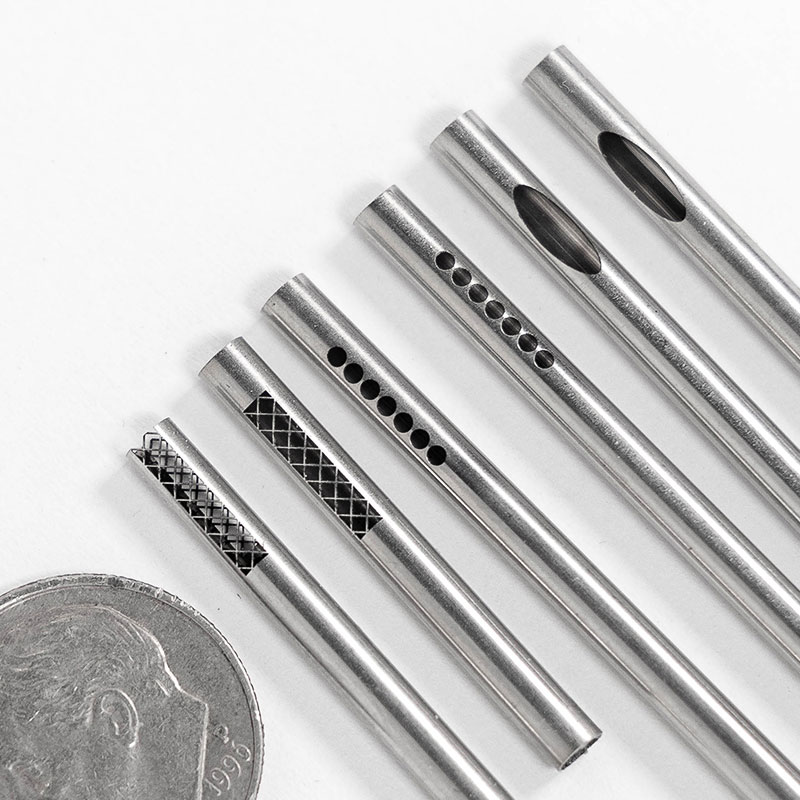
Discover The Potential of Ultrafast Lasers for Drilling
Laser drill and cut micro-tubing with no dross or slag, eliminating the need for post-processing.
Explore the Advantages of Laser Welding Plastics
By utilizing lasers for welding, devices such as microfluidic channel devices can be assembled, sealed, and integrated with high precision, ensuring the integrity and functionality of the microfluidic system. Learn more about the advantages of using laser technology for joining plastics
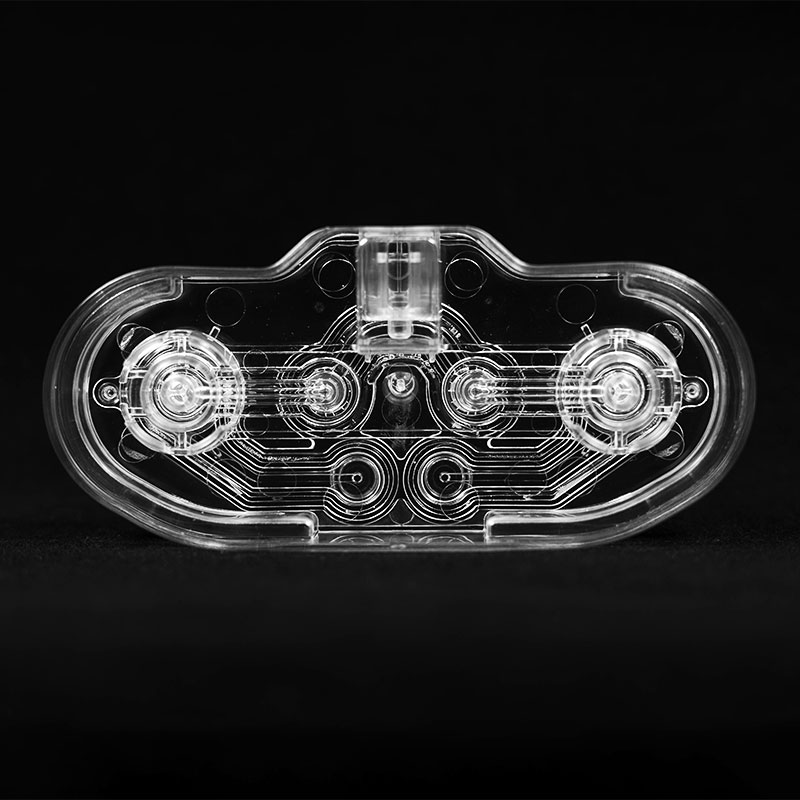
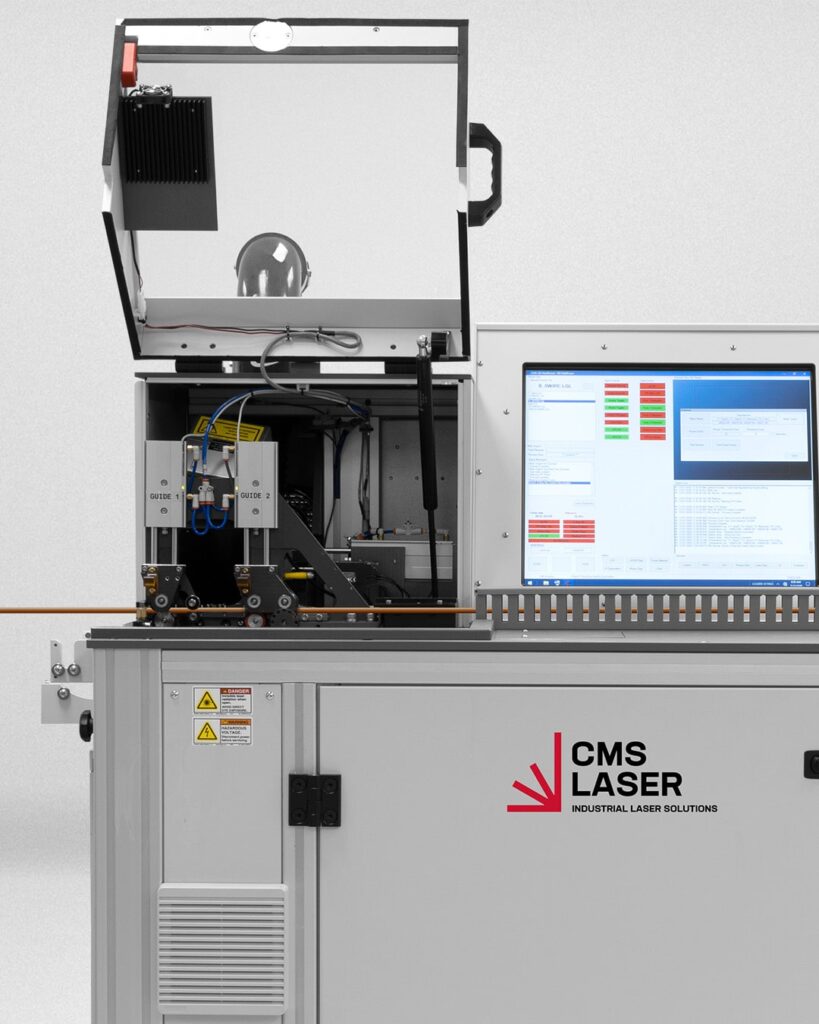
Laser Stripping Insulated Copper Magnet Wires
Discover this on-the-fly laser stripping machine we developed for removing insulation on enameled magnet wires for the medical industry. Remove polymers such as formvar, Kapton, polyimide and more utilizing a CO2 laser. Replace traditional acid baths and mechanical stripping methods with the power of focused beams of light.
- Clean and efficient laser ablation of polymer coatings
The Absolute Best Customer Service Around
Working with the entire Control Micro Systems team on our project was a pleasure. CMS was capable of meeting and exceeding our goals. They successfully designed and built a machine which increased our throughput by 550%! We are so glad we chose to move forward with CMS.
In the three years ACR has owned the CMS laser, it has worked flawlessly. In the few instances where ACR needed support in programming, CMS was quick to respond.
CMS have been excellent partners in the development of new, complex equipment for our business. CMS built multiple machines for us. Each machine had a different purpose, however the CMS team worked openly & honestly with us to agree on optimal solutions for each one.
Need Help Finding the Right Solution?
We don’t just build laser systems, we build partnerships.