Laser Processing Metal
Laser technology revolutionizes metal processing by offering precise solutions for marking, cutting, drilling, and welding. Laser marking creates permanent, high-contrast markings without additional substances. Cutting and drilling with lasers ensure clean edges and fine perforations, while welding achieves strong bonds with minimal heat impact. This technology sets new standards for precision and productivity in metal engineering.
- Ablation, oxidation, melting, or layer removal from various metals
- Cutting and perforating thin sheet metal with precision
- Welding metal tubing and creating hermetical seals with accuracy and efficiency
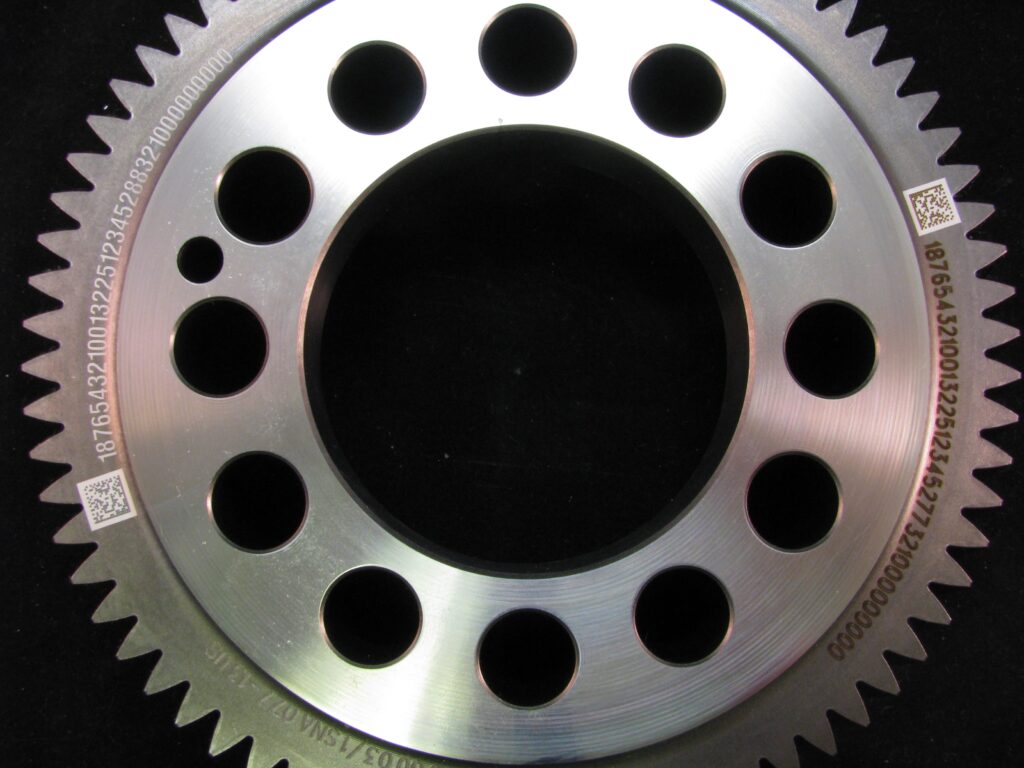
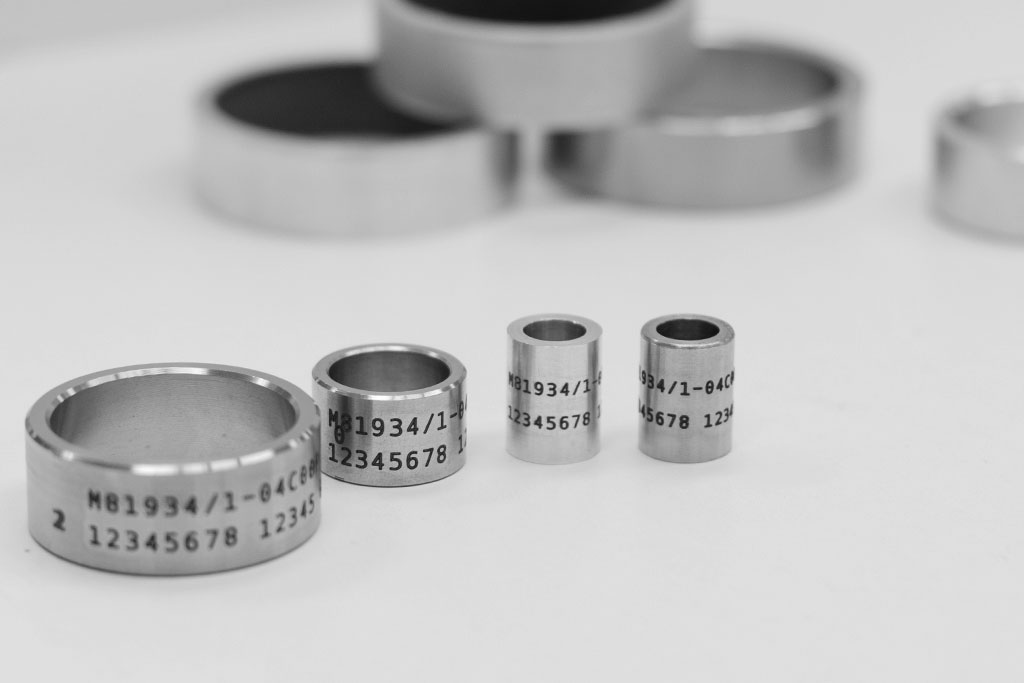
Mark, Cut, Drill, and Weld Metals
Laser metal processing offers unparalleled precision and efficiency in marking, cutting, drilling, and welding applications. In laser marking, a high-energy beam is directed onto the metal surface, causing a controlled oxidation or material removal, resulting in permanent, high-contrast markings.
For cutting and drilling, lasers provide precise and intricate control, delivering clean edges and fine perforations even on the thinnest metal sheets. By focusing intense energy into a concentrated spot, lasers swiftly vaporize or melt through the metal, leaving behind precise cuts and holes.
In welding, lasers create strong bonds by melting and fusing metal surfaces together with pinpoint accuracy, resulting in seamless joints and minimal heat-affected zones.
Laser Applications
From marking stainless steel oven panels to welding aerospace components, laser technology is a preferred method for high precision applications.
Laser Applications for Stainless Steel
Laser technology has revolutionized the processing of stainless steel, offering precise and efficient methods for marking, cutting/drilling, and welding. In automotive manufacturing, lasers mark part identification numbers and QR codes on components like engine parts and exhaust systems, ensuring seamless tracking and compliance. Similarly, in the medical industry, lasers are crucial for welding stainless steel components in surgical instruments and implants, ensuring high-strength joints with minimal heat-affected zones.
Additionally, lasers are utilized for cutting and drilling stainless steel sheets and components across various sectors, delivering unparalleled precision and efficiency while minimizing material waste.
Overall, lasers have become indispensable tools for high-precision processing of stainless steel components, meeting the stringent requirements of modern manufacturing.
Laser Applications for Titanium
Laser technology has profoundly impacted the processing of titanium, offering precise and efficient methods for marking, cutting/drilling, and welding, thereby enabling advanced manufacturing processes tailored to specific industry needs.
In the aerospace industry, titanium components such as turbine blades, engine casings, and structural elements undergo laser marking for part identification and traceability, while laser welding is utilized for joining complex aerospace structures with unmatched precision and strength.
In the medical field, titanium implants and surgical instruments benefit from laser marking for product identification and branding, ensuring patient safety and regulatory compliance. Laser welding plays a critical role in fabricating medical devices, where precision and biocompatibility are paramount, enabling the production of durable and reliable implants.
Laser Applications for Aluminum
Laser technology has emerged as a pivotal tool in the processing of aluminum materials, offering versatile solutions for various industries. With fiber lasers, manufacturers can efficiently mark logos, text, serial numbers, and other identifiers onto aluminum surfaces, ensuring precise and permanent markings.
Additionally, advancements in ultrafast laser technology enable the creation of high-contrast surface markings on bare aluminum without the need for additives. This innovative approach not only streamlines the marking process but also enhances the aesthetics and durability of aluminum components, catering to a wide range of applications across automotive, aerospace, electronics, and consumer goods industries.
Laser Applications for Brass
Laser etching has become a prevalent method for marking brass due to its ability to produce bold, dark markings, making it a popular choice across various industries. Brass, known for its durability and aesthetic appeal, finds widespread use in plumbing fixtures, jewelry, shell casings for ammunition, badges, signs, and more. With laser technology, manufacturers can achieve precise and permanent markings on brass components, ensuring product identification, branding, and customization.
This versatile application of lasers enhances the versatility and value of brass materials in diverse applications, from decorative pieces to functional components, meeting the demands of modern manufacturing and design.
Laser Applications for Copper
Copper, like brass, is a versatile metal utilized across a wide array of industries, ranging from electronics to cookware and beyond. With its excellent electrical conductivity and corrosion resistance, copper finds applications in electrical wiring, circuit boards, plumbing systems, cookware, architectural accents, and more. Laser technology offers a myriad of processing options for copper, including cutting, engraving, and marking.
Whether creating intricate patterns on electronic components or adding logos and identifiers to cookware, lasers provide precise and efficient solutions for enhancing the functionality and aesthetics of copper materials. This adaptability highlights the significance of laser processing in maximizing the utility and appeal of copper across diverse industrial sectors, driving innovation and versatility in manufacturing processes.
Laser Material Processing of Metal
Laser technology advancements has expanded capabilities in metal processing across industries
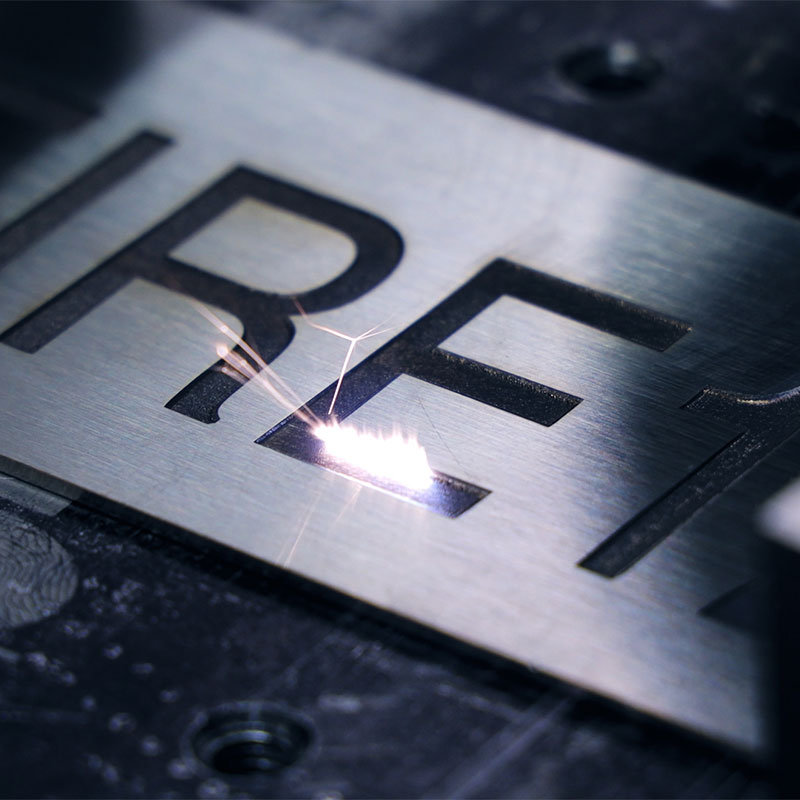
What Is The Difference Between Laser Marking And Engraving Metal?
Learn about the terminology our engineers use when determining the type of marking required.
Guide to Oxidation Laser Marking
Laser oxidation marking—also called annealing—is one of the most popular and effective techniques for marking metals.
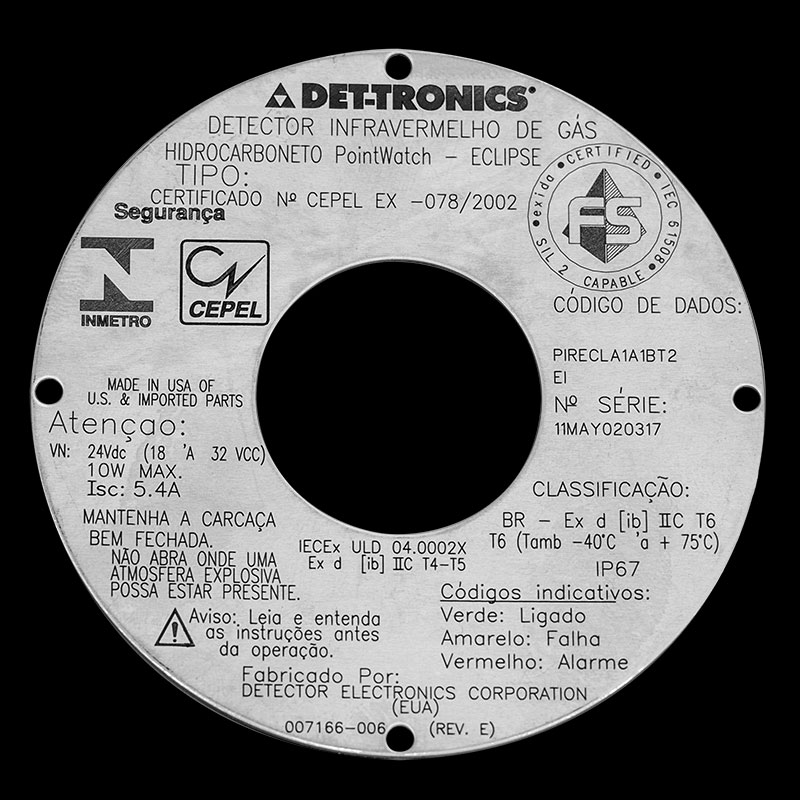
Discover Our Laser Systems
The Absolute Best Customer Service Around
Working with the entire Control Micro Systems team on our project was a pleasure. CMS was capable of meeting and exceeding our goals. They successfully designed and built a machine which increased our throughput by 550%! We are so glad we chose to move forward with CMS.
In the three years ACR has owned the CMS laser, it has worked flawlessly. In the few instances where ACR needed support in programming, CMS was quick to respond.
CMS have been excellent partners in the development of new, complex equipment for our business. CMS built multiple machines for us. Each machine had a different purpose, however the CMS team worked openly & honestly with us to agree on optimal solutions for each one.
Need Help Finding the Right Solution?
Send us your material to determine if your process is feasible