Creating permanent marks on organic materials like wood, leather or paper using laser technology is a common application. But when high production rates, complex automation and precision alignments are required, the job can become more challenging. At Control Micro Systems, Inc. (CMS), we can design and manufacture laser systems to overcome these challenges for any production environment using a variety of automation options.
General Considerations for Laser Marking
Using software-controlled galvanometer steering, the laser can mark or engrave text characters, linear barcodes, 2D data matrices, QR codes, logos and other graphics in almost any pattern onto wooden products. If designs are large and span beyond the laser scanning field of view, motion tables or other automated motion control devices can be integrated to cover the full area.
Laser marking and engraving quality will depend on the wood’s density, color and uniformity. Higher-density materials will need higher power or more time to ablate, while less-dense wood types will ablate faster and require less power. The color of the wood will determine the overall contrast of the laser marks. For example, lighter-colored wood will show higher contrast to the dark-colored mark areas. Marking across wood grain or any other inconsistencies in the surface will cause variations in the laser mark or engraving since the material can have different densities.
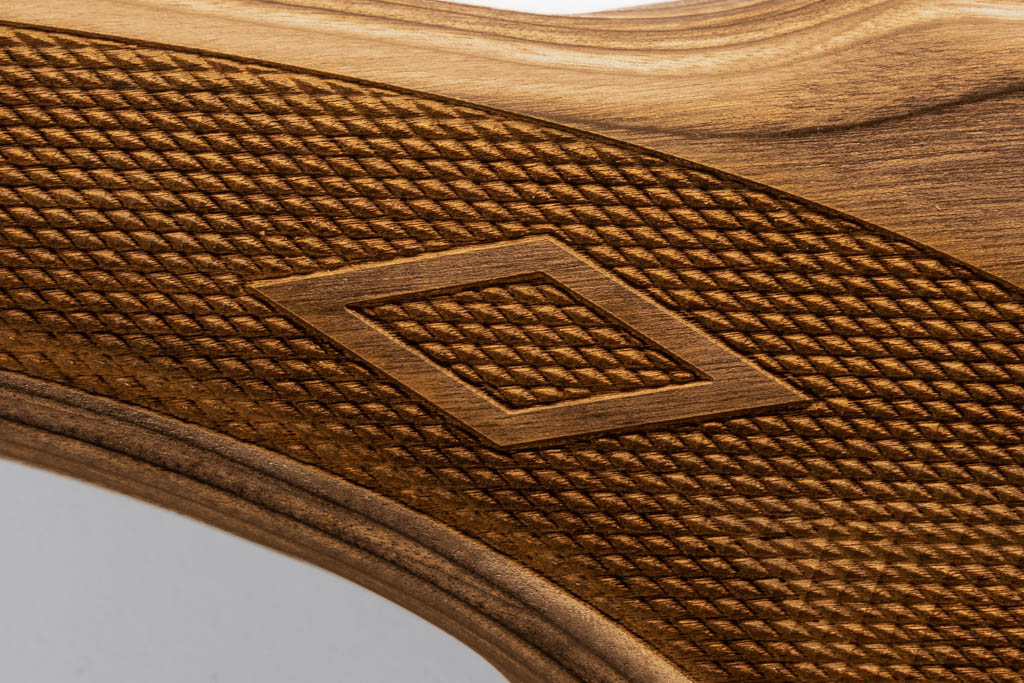
How to Choose the Right Laser
CO2 lasers are typically used for marking wood products. The far-infrared wavelength couples well with the wood, creating a controllable burning effect while keeping marking times fast and overall costs low. For surface marking, low-power lasers are used to lightly heat the surface of the part. The heat causes the wood to discolor and results in high-contrast, easily legible marks. For deep engraving, higher power lasers ablate the material directly while minimizing flames. A fume extraction system can pull the particulates away from the surface in a controlled manner.
Our Applications Lab can employ CO2 lasers ranging from five to 350 watts average power in order to provide samples of your marked or engraved wooden parts — no matter your requirements. The minimum line width for CO2 laser marking will be between 0.005 to 0.010 inches, depending on the wood being marked and the chosen focusing lens.
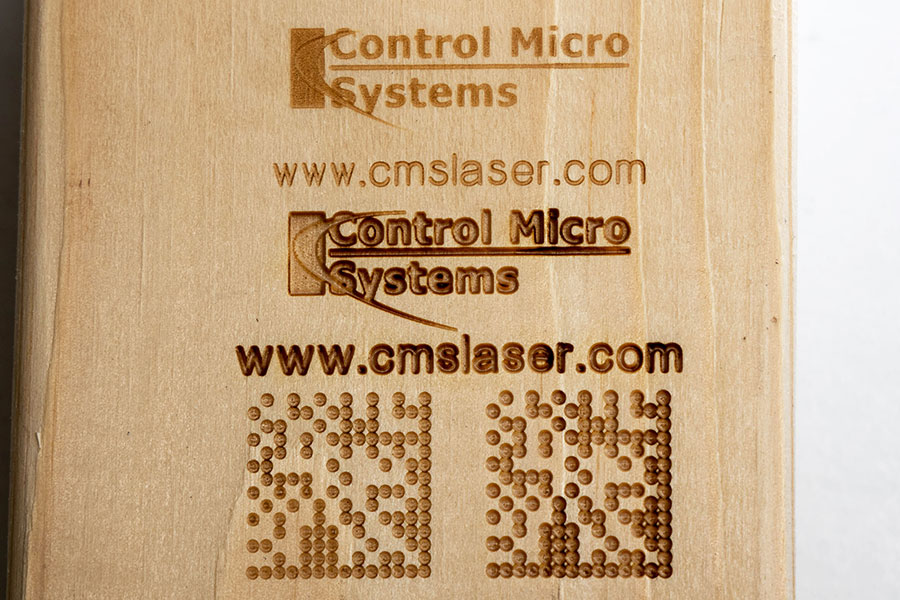
Other types of lasers can also mark and engrave wood with extremely fine details or minimal color contrast. Shorter-wavelength lasers allow for smaller laser spot sizes in order to create fine, intricate details, and they enable “cold-cutting” techniques that minimize wood charring during etching. These lasers come with increased cycle times and a higher overall cost, but they can also be used for special projects. If these requirements are important for your application, our Applications Lab also makes these lasers available to you to test.
Automation Options
Our wood marking and engraving laser systems can be configured to include virtually any automation required for your production needs. Some options include:
- Marking the wooden parts on-the-fly as they move on a conveyor.
- Using robotics to handle the parts for loading, unloading or motion required inside the system to mark or etch on multiple or rounded surfaces.
- Using a multiple-position rotary table system to mark or etch a tray of parts in one station while another tray is being loaded or unloaded at a different station.
- Inspecting a part using machine vision before marking or etching to identify part type and orientation, and to adjust the mark location and laser settings accordingly.
- Inspecting the mark or etching after completion to validate consistency and confirm the quality of the text, barcode or data matrix marks.
- Integrating depth sensors to track the depth of etchings during the process or to confirm depths after the process is complete.
- Using a handheld laser head, which is possible when low-power CO2 lasers are used, for quick identification marking or logo marking.
Contact our sales engineers today to discuss all automation options and to begin your free sample evaluation with our Applications Lab.
0 comments
Leave a comment.