Laser Drilling
Laser drilling is a non-contact process that uses focused, high energy density, light to ablate material and drill holes in a wide variety of materials.
Compared to other drilling methods, lasers offer superior speed and precision while lowering operating costs. As a result, they’re finding a home in a variety of industries, from automotive to medical device manufacturing.
They also play an important role in the pharmaceutical industry—drilling osmotic pump tablets at high speeds while maintaining extremely close tolerances.
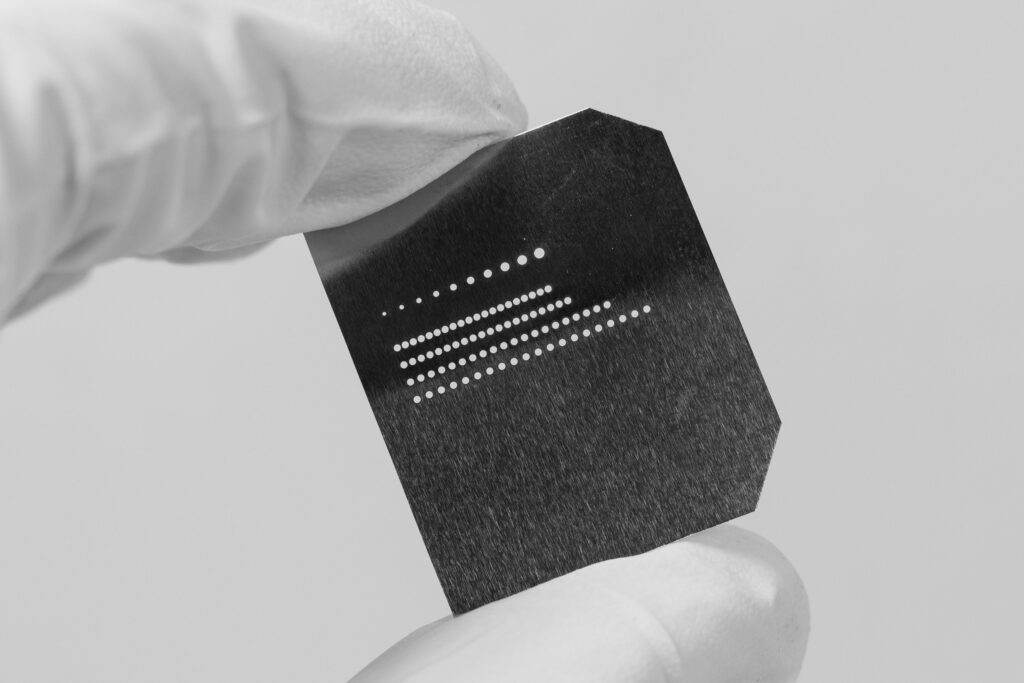
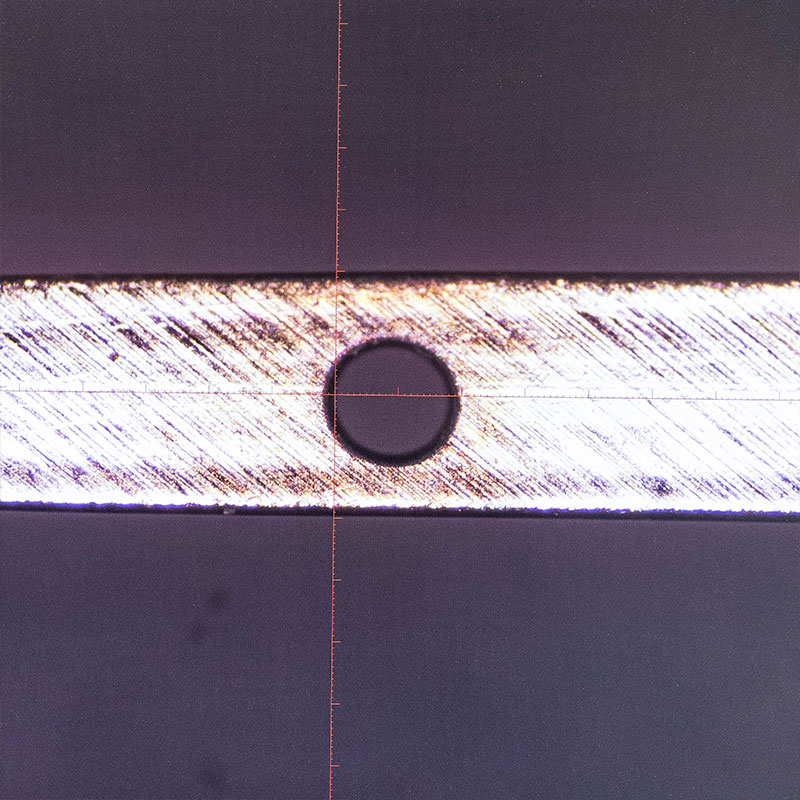
Laser Drilling Advantages
Laser drilling is a versatile material processing technique that offers numerous advantages. It can produce precise and accurate holes with diameters as small as a few microns and is a non-contact process that can be used to process a wide range of materials, including delicate or fragile ones. Laser drilling is also a high-speed process that can be easily automated, making it a cost-effective and efficient process for large-scale production. Additionally, laser drilling produces minimal debris and waste, making it a clean and environmentally friendly process.
Laser Drilling Capabilities
Laser Drilling Methods
The most basic laser drilling method is single pulse drilling—a simple, clean and fast process that has led to several variations, including:
- Single Pulse Drilling: One pulse of the laser is used to drill the hole. This is a simple, clean, and fast process when it is possible.
- Percussion drilling: This method is similar to single pulse drilling, but instead of using one large burst of energy, it uses several short, lower-energy bursts. Percussion drilling lets you create deeper, more accurate holes. Because less material vaporizes with each pulse, you can also drill holes with smaller diameters.
- Trepanning: A pilot hole is drilled through the material first using percussion drilling. The laser focal point is then scanned in a spiral shaped pattern starting from this pilot hole and increasing is diameter until the desired diameter hole is achieved. Most molten material is expelled downward through the pilot hole.
- Helical Drilling: Unlike trepanning, no pilot hole is drilled first. The laser is scanned in a spiral shape multiple times, removing a small amount of material with each pass, until the desired hole is completed. The focus spot can also be adjusted downward while the laser is drilling in this helical pattern to ensure the most efficient material removal at each depth through the material. In helical drilling most molten material is ejected upward out of the hole. This method is typically used to create deep holes with large diameters.
Laser Drilling Tablets
As a leader in the pharmaceutical industry, we specialize in designing and manufacturing laser tablet drilling systems that can efficiently produce holes needed for time-release medication. Our systems are capable of drilling small apertures ranging from 200 μm to 1 mm into osmotic pump tablets, achieving high speeds of up to 140,000 tablets per hour. This process enables us to create an infinite number of sizes and pattern variations, with the added ability to integrate vision capabilities for more precise control of aperture quality. Our drilling systems can also produce patterns or arrays of holes in a single tablet, and machine vision can be integrated to ensure that drilled holes are precisely controlled.
Overall, our laser tablet drilling systems offer an advanced and efficient method for producing high-quality time-release medication that meets the rigorous standards of the pharmaceutical industry.
Laser Drilling Plastic
Laser drilling is a highly effective method for processing plastic parts as it enables precise control over the shapes and sizes of holes without requiring any tooling changeovers. Unlike traditional drilling methods, laser drilling makes no mechanical contact with the plastic parts, minimizing the risk of material damage and allowing for greater flexibility in design. Our laser drilling systems are utilized in a wide range of applications, from spray nozzle valves to irrigation tape, and are particularly well-suited to producing small and intricate components.
Additionally, laser drilling can be easily automated for high-volume production, making it a cost-effective and efficient process for a variety of industries such as automotive, electronics, and medical devices.
Laser Drilling Metal
Our custom laser systems for drilling holes into metal components are utilized across a broad range of industries, including automotive and medical device manufacturing. The process can be applied to various types of metal, such as thin sheet metal, metal foil, and micro tubing, and is highly effective in achieving superior precision and accuracy. Laser drilling is a non-contact process that produces minimal heat affected zones and does not require physical contact with the material, which significantly reduces the risk of material damage. This results in a clean and efficient process that can be easily automated for high-volume production.
These advantages make laser drilling an ideal method for producing high-performance metal components used in critical applications such as aerospace, defense, and electronics.
Laser Drilling Ceramic
Laser drilling systems are highly effective at reducing strain on ceramic parts as they focus the beam’s energy into small areas. Compared to traditional drilling methods, they offer superior precision and reliability. With our laser drilling systems, it is possible to drill through-holes or partial holes for texturing or micromachining requirements. This technique can be applied to a variety of ceramic products, offering an efficient and effective method for processing ceramics in industries such as electronics, aerospace, and automotive.
Laser drilling is particularly well-suited to processing ceramics because it is a non-contact process that produces minimal heat affected zones and does not generate debris or waste. This allows for clean and precise drilling without damaging the delicate ceramic material. Additionally, the flexibility of laser drilling means that it can be used to create complex patterns and shapes with high accuracy, making it ideal for applications that require intricate designs. These advantages make laser drilling a popular choice in industries such as medical devices, where the production of ceramic components is critical for achieving high-performance products. Overall, the ability of laser drilling to offer precise and reliable processing with minimal damage to ceramics makes it a valuable tool for a variety of industries.
Discover our Laser Machines for Drilling
The Absolute Best Customer Service Around
Working with the entire Control Micro Systems team on our project was a pleasure. CMS was capable of meeting and exceeding our goals. They successfully designed and built a machine which increased our throughput by 550%! We are so glad we chose to move forward with CMS.
In the three years ACR has owned the CMS laser, it has worked flawlessly. In the few instances where ACR needed support in programming, CMS was quick to respond.
CMS have been excellent partners in the development of new, complex equipment for our business. CMS built multiple machines for us. Each machine had a different purpose, however the CMS team worked openly & honestly with us to agree on optimal solutions for each one.
Need Help Finding the Right Solution?
We develop solutions, solve problems, and create efficiencies.