Wire
Laser processing systems offers unmatched precision, flexibility and speed without damaging the insulation or sheathing. Mark text and symbols or strip wire insulation with ease and efficiency.
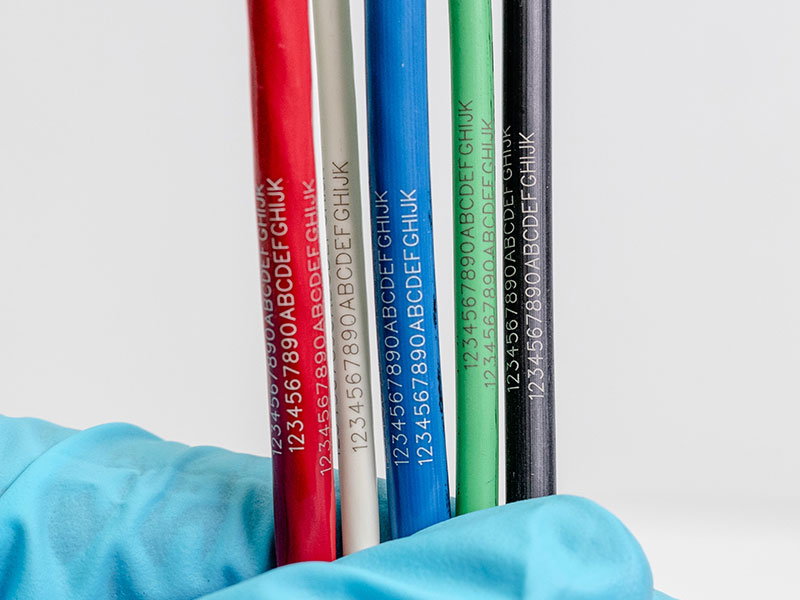
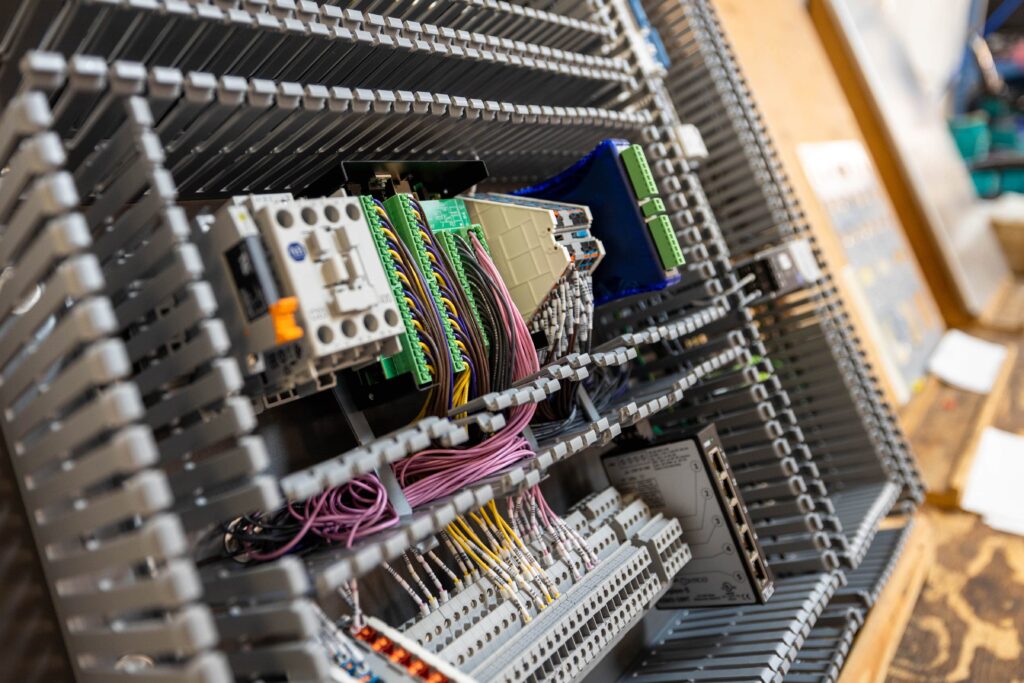
Strip and Mark Wire
Each year, billions of feet of cabling are installed around the world—requiring some kind of marking. Compared to other methods, laser wire marking offers unmatched precision, flexibility and speed without damaging the insulation or sheathing.
Mechanical, chemical and heat-based wire stripping methods require frequent cleaning, maintenance and adjustment and can also damage the conductor. Laser-based wire stripping overcomes these challenges. This non-contact approach keeps the conductive material and shield intact—eliminating weak spots for breakage or conductor resistance.
At CMS Laser, we’ll design a wire stripping system that meets your every production need. We can even combine wire marking and cutting processes within the same footprint—extending your capabilities without adding floor space.
Wire Marking and Stripping
The Advantages of Marking Wires with Lasers
Laser marking is the ideal solution for creating permanent wire marks that include manufacturing information and product identification. This flexible marking method easily adapts to product changes and does not require any consumables such as inks or masks.
Laser wire marking has become the gold standard for wire manufacturers globally because it meets all the necessary requirements. Laser wire marks are highly durable and cannot be scraped or rubbed off. Additionally, they share the same characteristics as the insulation material, making them capable of withstanding similar temperatures and flexing levels as unmarked wires.
Laser Wire Stripping Machines
Laser wire stripping is a highly efficient process that strips both sides of the wire simultaneously, minimizing wire movement and reducing strand variance. The laser’s wavelength is absorbed by the insulating material, while the metal reflects it, causing no damage to the conductive strand. This process enables the removal of wire insulation with high precision, reaching tolerances as low as 0.001 inches.
Our galvo-directed laser beams can move in any direction, providing complex wire stripping options. We offer versatile transport systems capable of handling wire and cable gauges ranging from 6 to 26. Our systems can also produce 200-foot lengths with less than 0.1-inch variance, ensuring optimal precision in the wire stripping process.
Our systems process most wire and cable types: round, twisted pair, flat, shielded, ribbon, coaxial and multi-conductor.
Lasers can also be used to strip thin polymer coatings on copper and aluminum (magnet) wires through an ablation process.
Our systems safely handle most insulating materials, including:
Enameled Coatings | Expoxy | ETFE |
Fiberglass | Formvar | Kapton |
Kynar | Milene | Mylar |
Nylon | Silicone | Polyester |
Polyesterimide | Polyethylene | Polyamide |
Polyvinylidene Fluoride | Polyurethane | Polyvinyl Chloride (PVC) |
Teflon |
Laser Wire Processing Videos
Laser Wire Processing Technology
Explore The Benefits Of Marking Wire Using UV Lasers
The marking of aerospace wires requires ultraviolet lasers due to their exceptional photochemical process. This process surpasses traditional fiber laser markings and guarantees zero damage to the wire insulation structure.
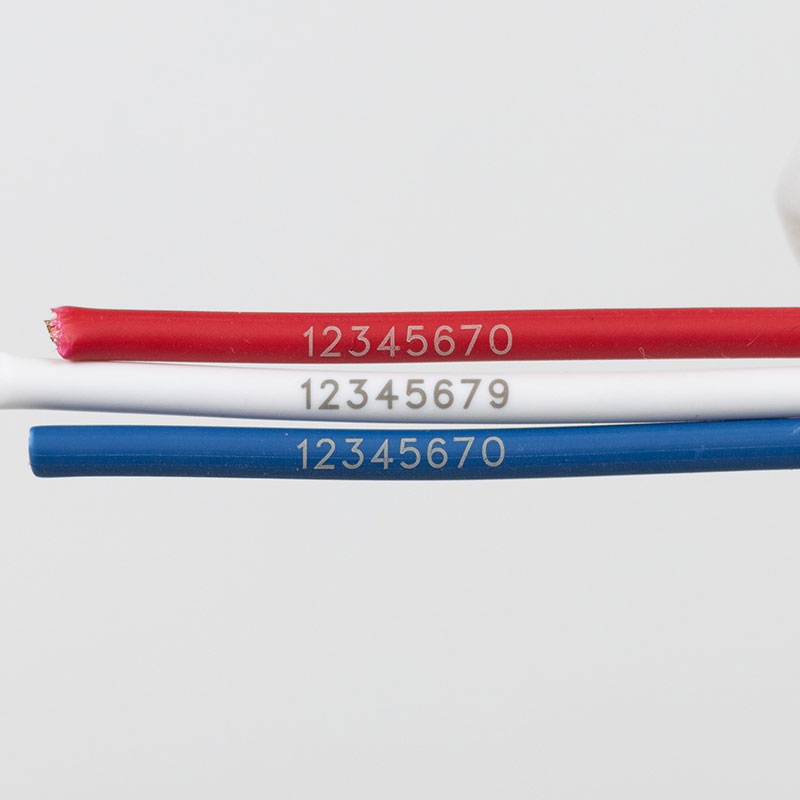
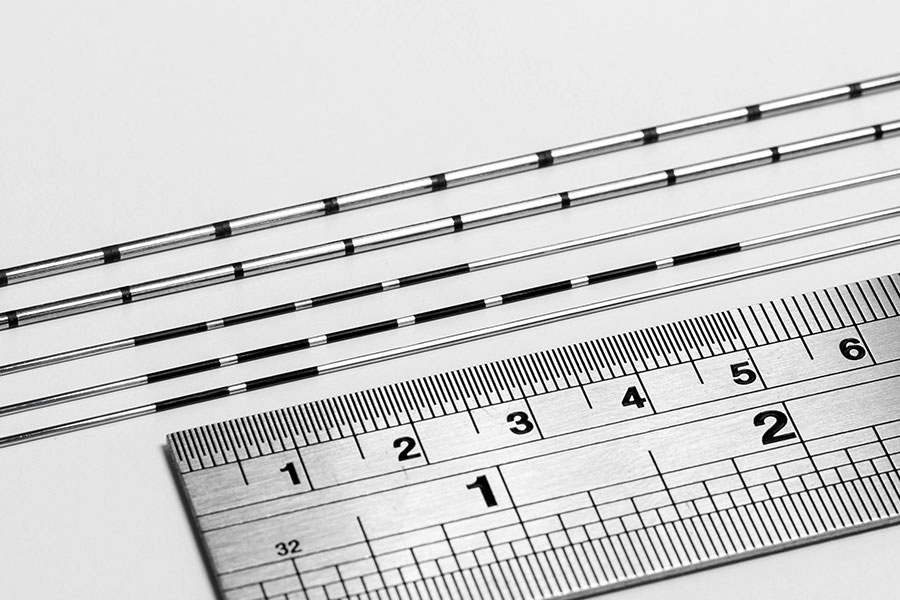
Laser Marking System For Medical Wires
Check out the stainless steel wire marking machine we built for Custom Wire Technologies, which improved their production efficiency by an impressive 550%! This state-of-the-art machine features an ultrafast picosecond laser marking machine and vision system, ensuring precise and accurate wire marking.
Laser Stripping Polymers from Magnet Wires
Discover our wire stripping solution, specifically designed to remove polymers from enameled wires. Our innovative solution allows for the stripping of wire coatings, such as formvar and polyimide, without the use of acids.
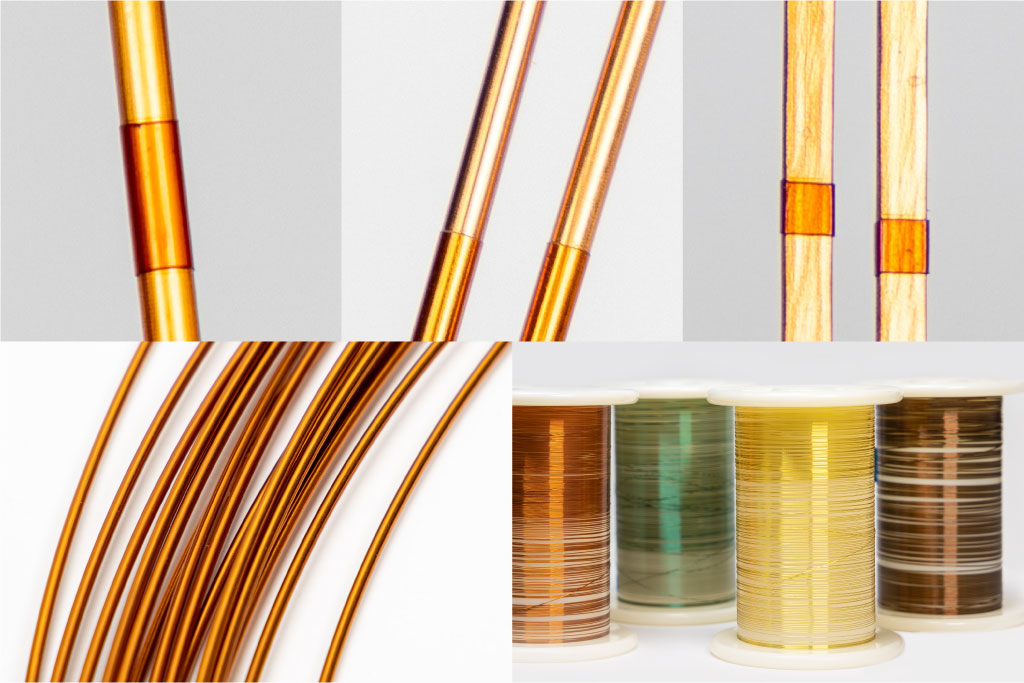
Discover Our Laser Systems
The Absolute Best Customer Service Around
Working with the entire Control Micro Systems team on our project was a pleasure. CMS was capable of meeting and exceeding our goals. They successfully designed and built a machine which increased our throughput by 550%! We are so glad we chose to move forward with CMS.
In the three years ACR has owned the CMS laser, it has worked flawlessly. In the few instances where ACR needed support in programming, CMS was quick to respond.
CMS have been excellent partners in the development of new, complex equipment for our business. CMS built multiple machines for us. Each machine had a different purpose, however the CMS team worked openly & honestly with us to agree on optimal solutions for each one.
Need Help Finding the Right Solution?
Send us your material to determine if your process is feasible.