Robotic Material Handling Laser Solutions
Our robotics integration can quickly and easily handle materials, making laser processing tasks more efficient and reliable in many different situations. Our industrial laser systems combined with robotic handling represent the future of laser material processing. They offer precise and adaptable part picking and path planning, improving productivity and increasing quality in modern manufacturing.
- Dynamic part positioning under laser focus
- High-speed material handling with vision assist
- Direct laser manipulation
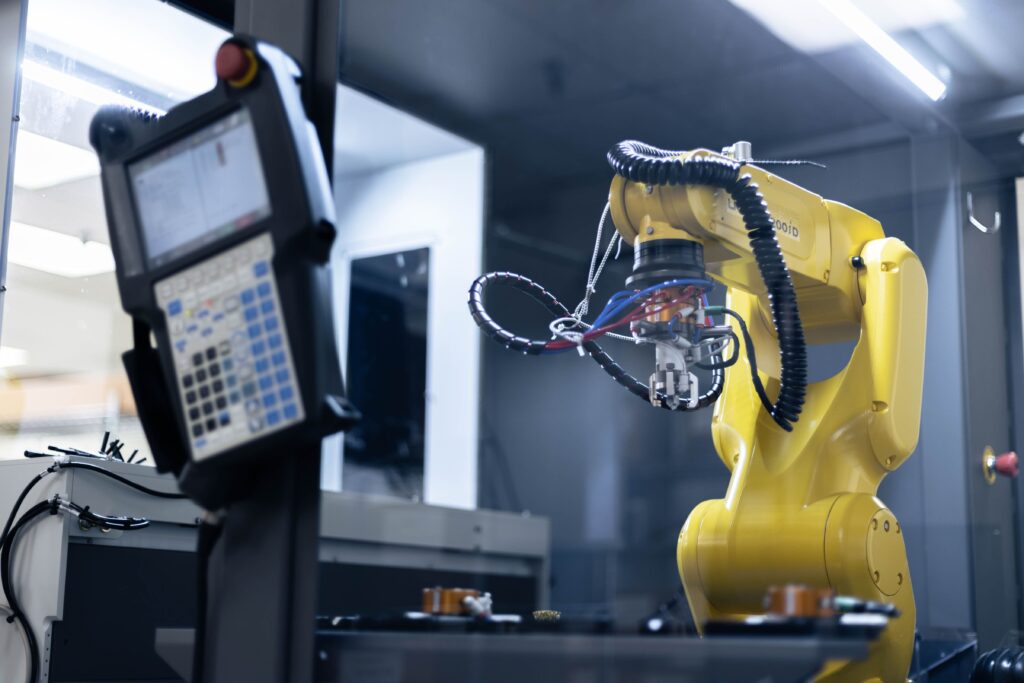
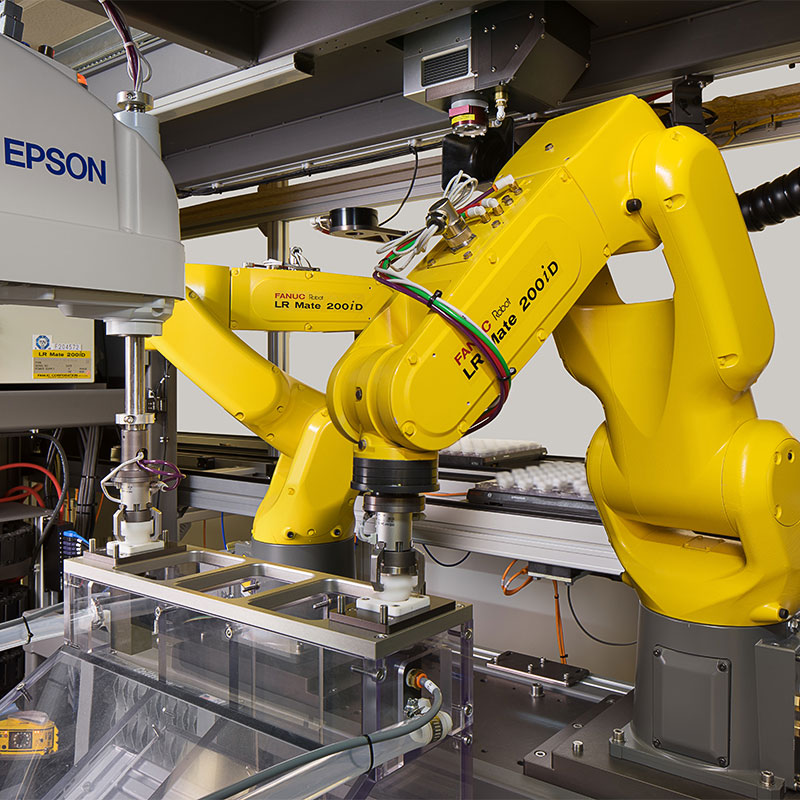
Material Handling Efficiency & Flexibility
The adoption of robotics within the material handling industry is steadily increasing year after year. A trend driven by companies’ ongoing efforts to minimize manual handling of components and streamline their processes. Our laser automation uses robots and machine vision to process complex objects with high accuracy and repeatability.
For maximum versatility in welding and cutting applications, the laser source can be attached directly to the robot’s end effector. This allows greater flexibility over a wide range of part geometries and sizes. We’ve also attached a vision camera to the end effector to guide pick and place procedures depending on feature detection.
Robotic Laser Processing Systems
Integration of Robots into Laser Marking, Cutting, and Welding Solutions
Robotics used for Automotive Laser Marking Tasks
Our engineers developed system for marking automotive parts on pallets. This system uses a conveyor, a 6-axis robot, a rotary table, and a (TTOV) vision camera. Parts arrive on pallets through a conveyor belt on the left side of the system.
The robot’s task is to pick a part from the pallet and place it onto the rotary table fixture. After laser marking the part, the robot will place it back into the pallet. Should a part not meet validation criteria, the robot removes it from the fixture and places it into the reject chute.
- Fully automated UID laser marking process
- Robot loads a new part onto the rotary table as one is being processed
- Post-process vision validation of laser marked data matrix
Automated Laser Drilling using Robots
Utilizing a combination of two 6-axis robots and a SCARA robot, this laser drilling system efficiently handles plastic components. Robots excel at managing complex part geometries, making them the perfect fit for the task. Our engineers programmed the system to achieve both speed and precision in drilling a range of plastic components.
- Two 6-axis FANUC robots
- High-power CO2 laser mounted to ceiling
- CCTV camera for process monitoring
- Pallet conveyor for loading parts into the system
- Testing station with SCARA robot for part handling
Robotic Part Handling for Laser Marking Plastic
Robots offer a smart solution when dealing with a variety of part shapes and sizes. With a 6-axis robot, you can smoothly manipulate and rotate parts in front of the laser, streamlining the marking process. This removes the need for complex setups, making the whole procedure faster.
Furthermore, programmers can program robots to handle new part designs. For less popular LEDs, our engineers included a rotary fixture stage in front of the laser to handle low volume production.
- Efficient part handling accuracy and speed
- Rotary unit for marking larger LEDs
- Reprogrammable for different parts
SCARA robots for Wafer Serialization
Our wafer marking solutions utilizes a high-performance 4-axis SCARA wafer robot for wafer transportation with a pre-aligner for positioning.
The robot moves the wafer to a pre-aligner. Then, it moves the wafer into the laser enclosure. The purpose is to add a special serial number, or unique identifier, for tracking purposes. Leveraging their impressive speed and unmatched precision, these robots enable us to engineer efficient wafer marking laser systems for serialization.
- 4-axis SCARA wafer robot
- Wafer pre-aligner for mark positioning
- Post-process machine vision verification of marked serial numbers
Laser Cutting Plastic Tubes
Lasers are also great at holding parts in front of the laser to perform marking and cutting tasks. In this example, our engineers utilized a 4-axis SCARA robot for cutting plastic injection molded medical test tubes. The robot acts as a rotating fixture for cutting the cylindrical parts.
By utilizing robotics, our engineers effectively reduced the complexity of handling the test tubes. By changing the end effector and software, one system can cut various tube sizes easily. Our engineers also designed the enclosure to fit a conveyor, completely automating the whole process.
- Can laser cut multiple tube sizes
- Robot end effector change over station
- Designed for adding a conveyor through the system for full automation
Related Videos
Robotic Part Handling Solutions
Discover these laser marking systems utilizing robotics
Machine Vision Assisted Robots
Our robotic solutions can utilize an off-axis vision system for detecting part orientation for the robot. Vision identifies distinct features on the object, allowing the robot to rotate and position the mark accurately. This technique eliminates the need to place parts in specific orientations and drastically improves the manufacturing process altogether.
- Part orientation detection and correction
- Dynamic process guidance
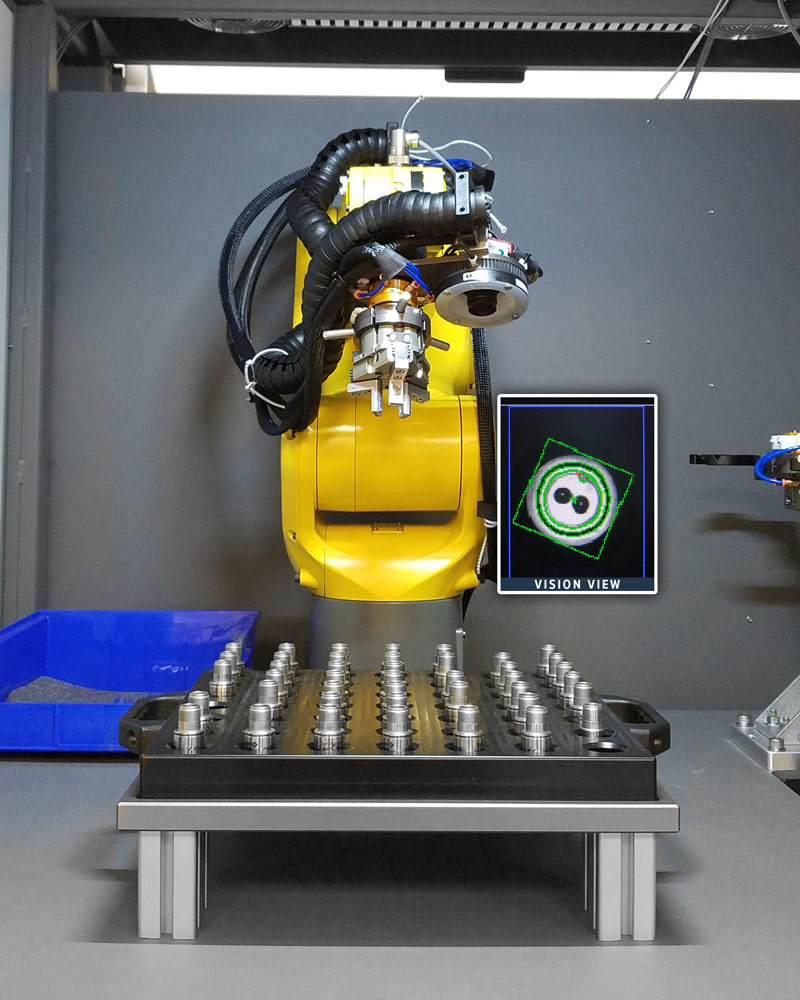
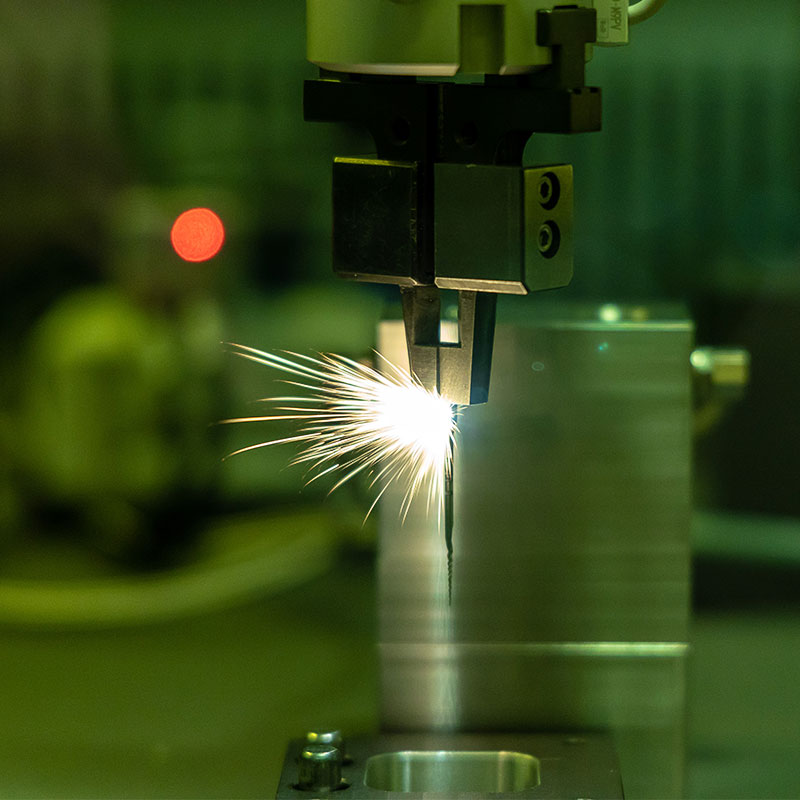
Titanium Drill Bit Marking Solutions
Robots not only made this process possible but reduced the overall footprint and complexity of this system. Different sized bits can be marked with a simple changeover of the program.
- Fast, efficient and precise
Robotic Part Handling
Difficult to handle products often benefit from robotic material handling. Robots can utilize machine vision techniques for high-precision pick-n-place actions, enabling advanced material processing.
- Two machine vision systems
- Post-process marking validation
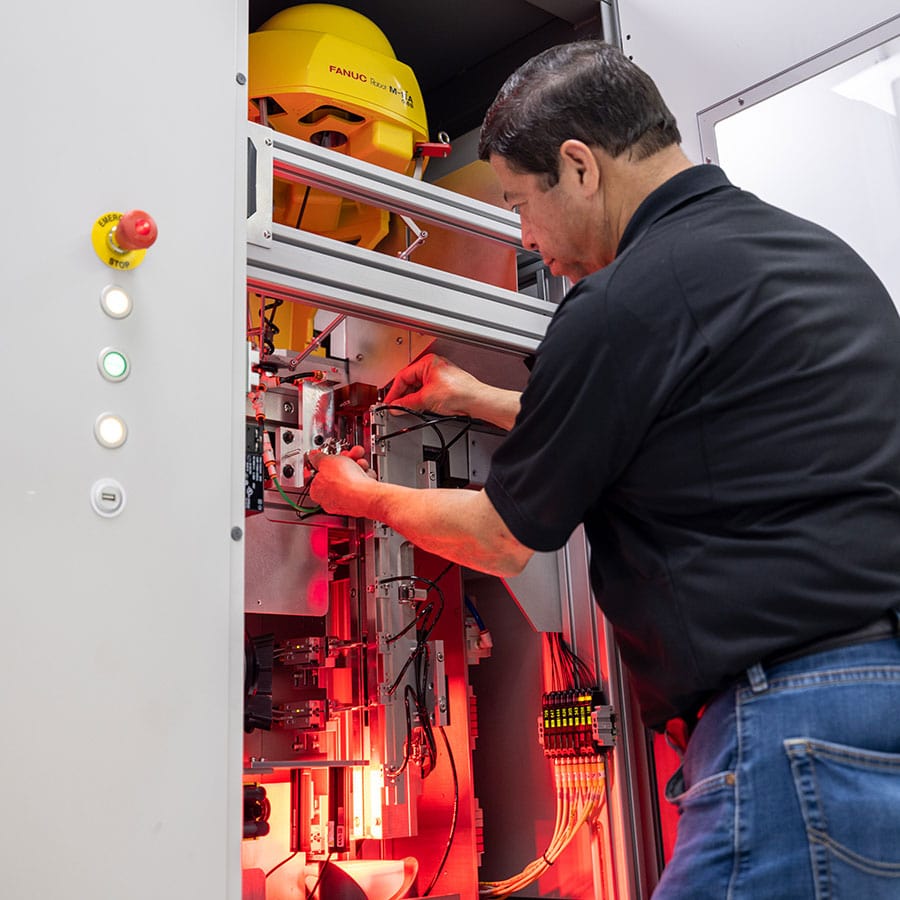
The Absolute Best Customer Service Around
Working with the entire Control Micro Systems team on our project was a pleasure. CMS was capable of meeting and exceeding our goals. They successfully designed and built a machine which increased our throughput by 550%! We are so glad we chose to move forward with CMS.
In the three years ACR has owned the CMS laser, it has worked flawlessly. In the few instances where ACR needed support in programming, CMS was quick to respond.
CMS have been excellent partners in the development of new, complex equipment for our business. CMS built multiple machines for us. Each machine had a different purpose, however the CMS team worked openly & honestly with us to agree on optimal solutions for each one.
We Partner With You
To develop solutions, solve problems, & create efficiencies.