In the majority of industries, products need to display distinctive markings, such as logos or part numbers. Traditionally, this has been accomplished through methods such as ink-based procedures or dot peen marking among other techniques. However, lasers have become the preferred technology for marking data due to their versatility in marking various materials, low maintenance, and ability to function efficiently in high-speed manufacturing environments for extended periods.
The Laser Marking System
Our expert engineers have designed and developed a rotary table laser system specifically for branding saw blade stacks with product logos and important usage information. The stacks can weigh up to 50kg, making it possible for an operator to process a large volume with just one button press. Our engineers have programmed a wide range of blade sizes, enabling the customer to effortlessly switch between programs, load parts and start laser marking by simply turning the key and selecting a program. The system is designed to operate in a “lights out” environment.
The laser source for this machine comes from a trusted business partner. Our partner had previously supplied manual loading systems but lacked the engineering capacity to fully automate the process. That’s where CMS Laser steps in, offering a tailored turnkey solution through our collaboration. As specialists in such requests, CMS Laser successfully designed and constructed the machine, utilizing the laser source selected our trusted partner.
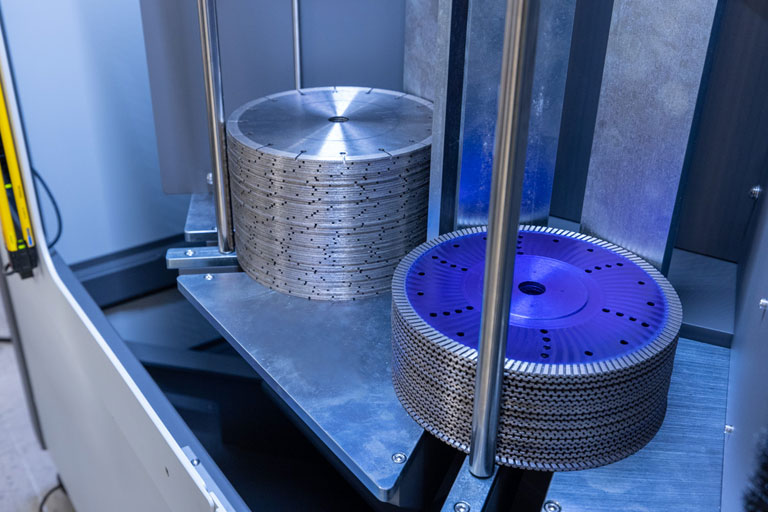
Machine Vision for Laser Process Alignment
The system leverages our Through-The-Optics Vision (TTOV) technology for precise placement of graphics on the blade. The camera is positioned in line with the laser beam as it exits the laser scanhead, offering a highly accurate top-down view of the part. The software has been calibrated to recognize the center hole of the blade, thereby updating the positional coordinates of the graphic. The CMS Laser software will alert the operator if the camera fails to recognize the center of the part.
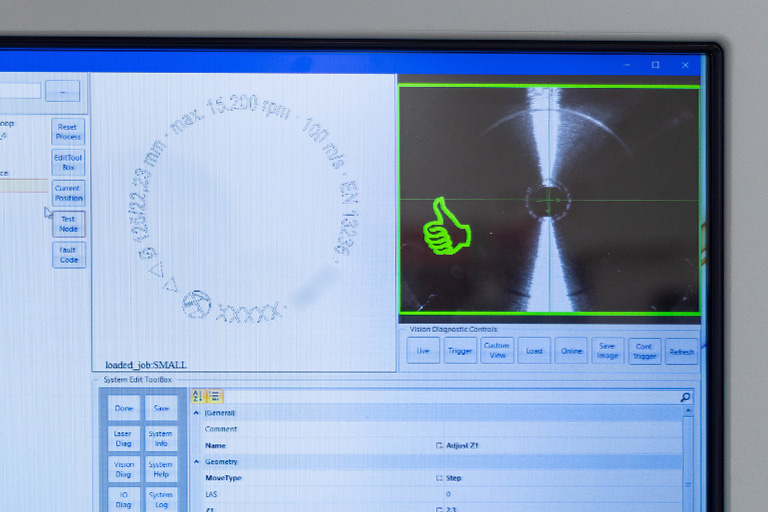
The Benefits of Integrating Machine Vision in Laser Material Processing
Machine vision is used in our industrial laser material processing machines to improve the accuracy and efficiency of laser marking, cutting, and welding processes. It is implemented by integrating a camera and image processing software into the laser system. Below are some ways CMS Laser utilizes machine vision.
- Robotic Automation – Monitor part orientation and position to adjust a robot’s XYR coordinates. This robot laser marking machine uses vision to detect the rotation of a part in a pallet before processing.
- Image Analysis – The camera captures images of the material and the software analyzes the images to detect features such as edges, patterns, and specific points. This information is used to control the laser beam’s position, ensuring that the laser markings are placed precisely on the material. Vision can also be used to determine if there is a part present or not. This laser cutting machine for plastic degating is a great example of a system using edge detection to align each cut location for separating injection molded plastics.
- Quality Control – Checking for defects and ensuring that the laser process is performed within specified tolerances. This is especially useful in laser welding applications.
- OCR / OCV – Recognize and validate characters or symbols before or after laser processing.
CMS Laser Solutions
This project showcases the proficiency of CMS Laser. As specialists in laser solutions, our company offers custom turnkey solutions throughout its 40-year-old history. With a proven track record of surviving tough economic times since 1983, CMS Laser provides a distinct engineering advantage in the industry. If you seek an engineering partner for laser material processing, reach out to our team to discover the possibilities.
0 comments
Leave a comment.