Laser marking of plastics has become common in industrial equipment, medical devices, aerospace components, automotive parts and common household appliances. However, medical device manufacturing (MDM) suppliers are required to track their products using unique device identification (UDI) codes, data matrices and other tracking information. They must also meet strict Food and Drug Administration (FDA) and GS1 guidelines. If a rare malfunction or other adverse event takes place, tracing a product to where and when it was manufactured goes a long way toward recognizing what went wrong and taking action to prevent it from occurring again.
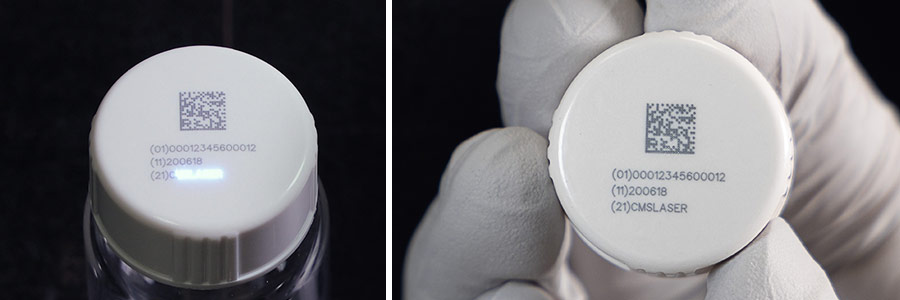
“Cold Marking” with UV Lasers Delivers a Smooth Mark within Surfaces
When marking plastics, first consider the type of marking that’s needed. Methods range from surface melting or foaming, to photochemical alteration of the material using ultraviolet and green lasers. For medical-grade plastics, UDI markings must be smooth to the touch, eliminating areas where bacteria may build up. This is where “cold marking” with ultraviolet wavelengths comes into play. Using UV lasers in the cold laser marking process alters the molecular structure of the material, which is desirable for applications sensitive to thermal damage. This thermal damage outside the marking area is referred to as the heat affected zone (HAZ). Additives in white plastics, such as TiO2, strongly absorb UV light and undergo a chemical change in the plastic, turning it dark. This process produces a smooth, highly legible mark within the plastic, rather than just at the surface.
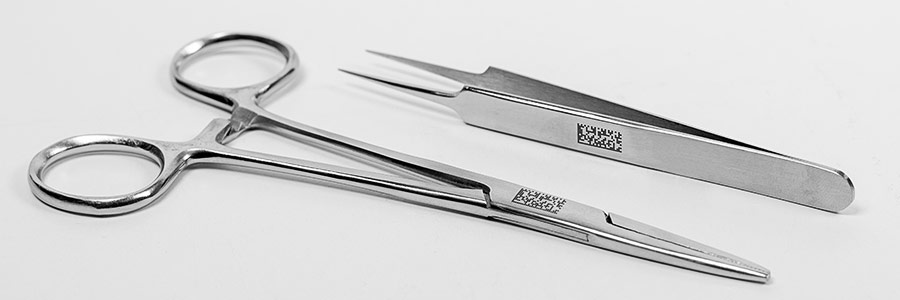
Ultrafast Lasers for Manufacturing Medical Devices
Using a new arsenal of ultrafast lasers — picosecond and femtosecond pulse widths — we developed systems to perform processes that will not damage a medical device’s surface, allowing it to withstand consistent cleaning and daily use. For devices that require cutting or drilling, the short pulse widths of ultrafast lasers produce minimal acceptable HAZ, enabling manufacturers to develop devices with cleaner micro holes and cuts. These lasers are perfect for plastics such as high-density polyethylene (HDPE), Delrin®, nylon and Teflon® (PTFE). Devices made from metal also benefit greatly from ultrafast lasers by offering the same level of quality — smooth surfaces, micron-level HAZ, mark durability and superior quality over traditional methods — making them perfect for implantable devices and surgical tools.
At CMS Laser, we have extensive experience in the medical device industry and have developed advanced solutions for laser marking, cutting and drilling applications.
Reducing Costly Manufacturing Errors with Laser Automation
Not only is the quality of the process important for MDM applications, but incorporating vision and automation systems can reduce manufacturing errors and contribute significantly to comprehensive quality assurance. We built our reputation on utilizing machine vision for reducing costly manufacturing errors by verifying the part, aligning the application and post-verifying the process and data. Full automation with robots and conveyors also eliminates human error and boosts overall production.
Free Material Testing
We encourage companies to send us their materials for feasibility testing to determine the best possible laser configuration and optics for the job. Get started today to find out why companies turn to us for solving complex, high-precision manufacturing challenges with laser-focused engineering.
For more information about cold marking medical plastics with UV lasers, contact us.
0 comments
Leave a comment.