Lasers are precise, flexible and clean—making them an ideal tool for medical applications like catheter manufacturing. From cutting stainless-steel guide wires to marking text on plastic parts, lasers do it all with minimal heat and post-processing.
Let’s explore the various laser processes found in catheter manufacturing—marking, welding, cutting and drilling—as well as the benefits laser systems bring to the medical industry.
Laser Marking Plastic Catheters
Lasers for marking polymers range from far-infrared to ultraviolet wavelengths, depending on the material’s chemistry and absorption spectrum.
Lasers with a 1,064-nanometer wavelength or shorter create a color change in the surface of the plastic. This change—often caused by a chemical reaction in the polymer—makes the contrasting marks durable and highly visible.
In addition, short wavelengths allow for smaller spot sizes, enabling you to make precise, detailed marks on the catheter side wall. The resulting label, text or logo easily meets the tight tolerances required by the medical industry.
Laser Welding Catheter Assemblies

Plastic welding is a common laser application that has many uses in the medical and catheter industry. Laser welding uses a focused beam to tightly control the position of heat being applied to the part, reducing the heat affected zone around the weld area.
Welding methods include:
- Transmission welding. This process involves welding two layers of plastic together: the top layer transmits through the laser-specific wavelength, and the lower layer absorbs it—melting the interface between the two layers. This type of welding typically involves near-IR wavelengths.
- Heat conduction welding. This method—which involves melting two plastic parts and fusing them together—is useful when both parts absorb the same laser wavelength. Typically, a CO2 laser is used.
- Clear-on-clear welding. This method utilizes a non-standard fiber laser to weld two transparent plastics without any additives or color changes. The laser transmits through the top layer, interacts with the interface between the layers and then heats the seam from the interface—achieving precise heat control.
Cutting and Welding Braided Stainless Steel

Manufacturing catheter guide wires involves cutting them to length while welding the braided ends—a difficult process to automate. Fortunately, both processes can be combined into a single laser system with no added materials or post-processing required.
The high-energy density of the focused laser beam ablates the stainless steel to cut it. At the same time, the heat is controlled at the cut ends—preventing the strands from unraveling. Melting the ends in this way makes them smooth and dimensionally consistent.
Laser Drilling Holes in Catheters
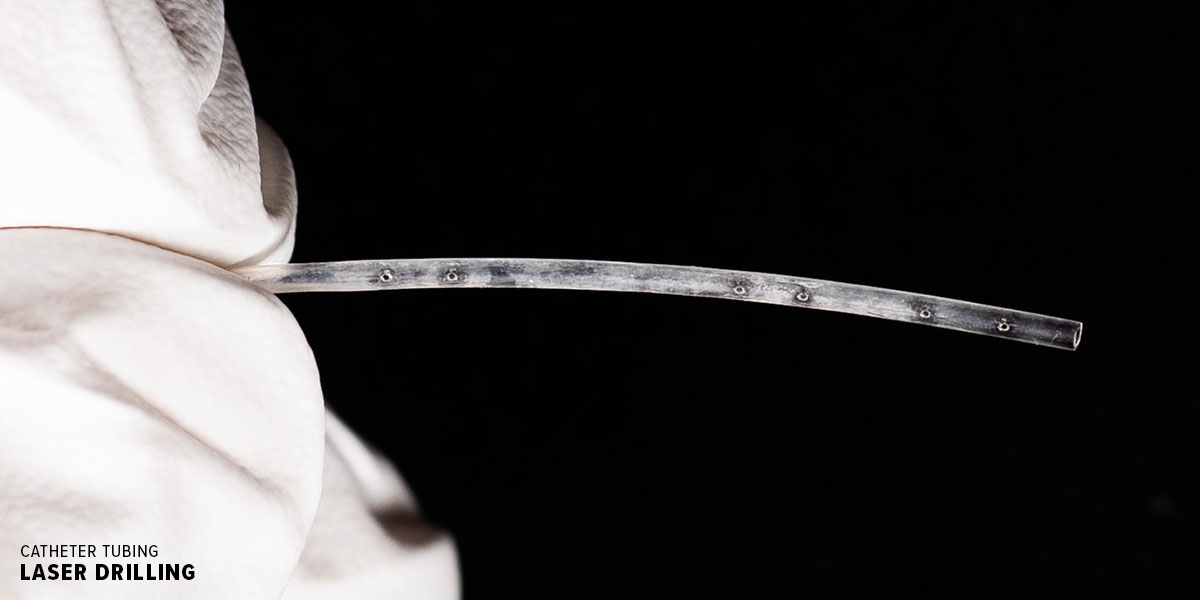
Lasers can be used to drill holes and eyelets in catheters with specific shapes and dimensions—all while minimizing the heat affected zone and taper.
These applications usually utilize UV lasers—355 or 266 nanometers—which ablate the material before it can melt too much, reducing the overall heat in the part.
Ultrashort picosecond or femtosecond lasers can be used if the application requires strict quality tolerances or minimal heat. For less precise applications where more melting can be tolerated, CO2 lasers are a solid, low-cost alternative.
Learn More
At CMS Laser, we have extensive experience designing and manufacturing laser systems for the catheter industry—no matter your need. For free sample development and analysis, contact our Applications Lab today.
0 comments
Leave a comment.