Rapid advancements in the medical industry are leading to smaller, less-invasive instruments, with correspondingly reduced feature and aperture sizes. While device manufacturers can choose from various drilling methods, ultrafast lasers (picosecond and femtosecond) for drilling is the best choice for exacting quality control requirements and demanding production goals. Some of the devices that can benefit from this technology include: drug delivery balloon catheters, intravesical drug delivery, micro-catheters, cardiovascular embolic filters and microneedles (transdermal drug delivery).
Cleaner Holes Means No Post-Processing, More Design Choices and Lower Production Costs
Drilling medical devices with ultrafast lasers has all the typical advantages of laser drilling over conventional methods, including:
- Non-contact Process. Laser drilling eliminates cleaning, sharpening and replacing bits and other parts.
- Flexible. Depending on the application and material, hole shapes and sizes can be tuned via simple software inputs.
- Taper Control. Control taper and chamfers with precise micromachining of sides and hole edges. Specialized optics can also create zero taper and reverse tapers.
- On-the-Fly Processing. Drilling holes while parts are moving increases productivity, speed and flexibility.
Ultrafast drilling also offers unique advantages over traditional nanosecond and microsecond lasers, such as:
- Multiphoton Absorption. Unlike longer pulses where the photon energy of the laser wavelength must match the band gap in the material for efficient coupling, ultrashort pulse lasers can overcome the band gap energy by multiphoton absorption. Longer wavelengths (i.e., NIR) can be used with materials that previously required frequency doubled (green) or tripled lasers (UV).
- No Post-Processing. The top and bottom edges of holes will be smooth. No grinding or polishing is required to remove raised edges.
- Minimized HAZ and Mechanical Stress. When performed correctly, damage or modification of the substrate due to heat transfer extends only microns into the substrate. Holes can be placed closer together without affecting each other.
- Self-Focusing/Filamentation. Deep penetration in transparent materials is possible due to the interplay of induced change in the refractive index (focusing) and plasma generation (defocusing).
- Mostly Material Independent. With ultrafast lasers, almost all materials can be processed with minimal mechanical and thermal damage. For plastics that are mostly transparent to visible and NIR ultrashort pulses, UV ultrafast lasers are required.
- Deep Holes. Holes with aspect ratios greater than 20:1 are possible.
Ultrashort laser drilling uses similar methods to traditional laser drilling:
- Percussion Drilling. Small diameter holes are drilled with a single pulse or multiple pulses with no translational movement of beam or part. Typically, the minimum hole size is controlled by the diffraction limit of the laser wavelength and focal length. Ultrashort pulses have the potential to drill holes smaller than the diffraction limit in some materials.
- Trepan Drilling. Percussion drilling is used to pierce a central hole; then, the beam is spiraled out in a single pass to cut to the desired diameter. Given the relatively low power of ultrafast lasers, especially femtosecond lasers, this method is mostly used on thin materials.
- Helical Drilling. Helical drilling cuts around the outside diameter of the hole using multiple repetitions (and possible motion in the Z-direction) to slowly deepen the cut depth. There is no piercing hole. Once the hole is pierced, there may be some “clean-up” passes. For holes more than two and half times the kerf width, a slug will be left over after drilling.
- Micromachining (Ablation). A variation of helical drilling, micromachining uses multiple repetitions and complete surface ablation (spirals, serpentines, raster passes) of each layer to “drill” round holes or other shapes. In tapered holes, the hole shape can be programmed to change with depth. Tapers, steps, chamfered edges and rounded edges are well controlled.
Select Control Micro Systems Applications:
Drilling Stainless Steel Microtubing
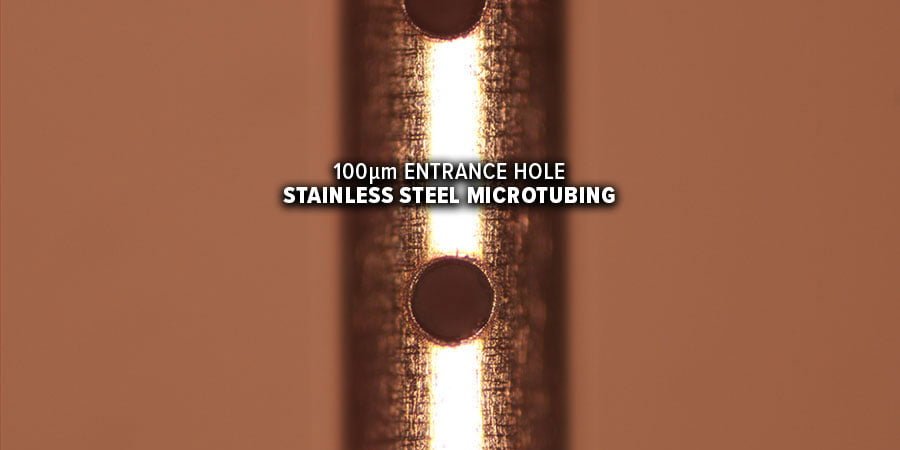
- Goal: Drill the cleanest and most accurate hole possible without damaging the opposite side of the tube. No post-processing allowed.
- ID of tube = 178 µm; Hole size = 100 µm; Drill time = 7.4 seconds.
Drilling Braided Polyimide Medical Tubing
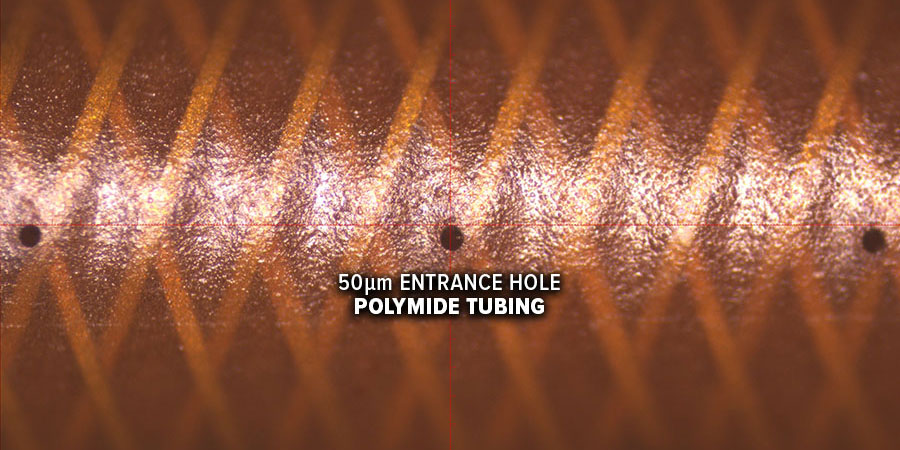
- Goal: Drill holes along the length of a one-meter tube. Drill only in polyimide areas between the stainless steel braid. Do not char, melt or damage the area around the hole or on the opposite side of the tubing. No post-processing allowed.
- The ideal drill location and braid sometimes overlapped. Through-the-Optics Vision (TTOV) was used to adjust the location and avoid drilling the stainless steel.
- ID of tube = 1900 µm; Hole size = 50 µm; Drill time = 0.2 seconds.
Drilling Nylon 12 Catheter Tubing
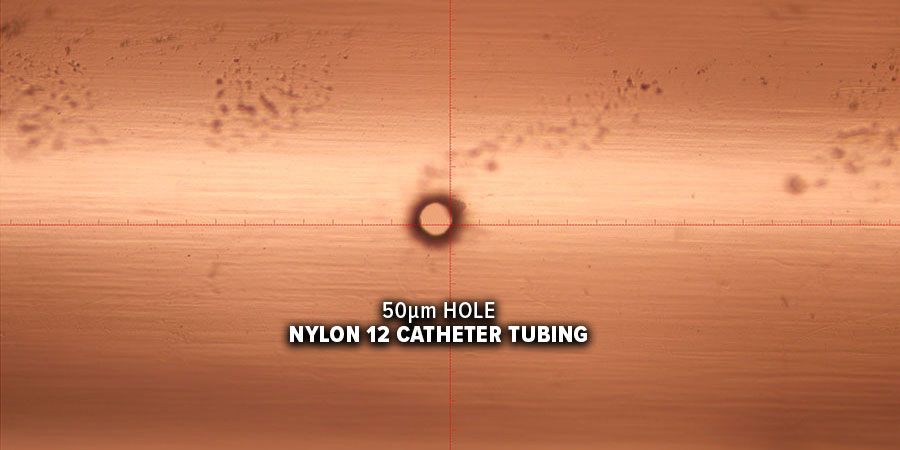
- Goal: Drill the cleanest and most accurate hole possible without damaging the opposite side of the tube. No post-processing allowed.
- ID of Tube = 760 µm; Hole size = 50 µm; Drill time = 0.6 seconds.
As medical instruments continue to get smaller and more complex, ultrafast laser drilling has become an attractive option for manufacturers looking to create precise, micro-sized holes with no post-processing. CMS Laser’s ultrafast laser drilling capabilities enable manufacturers to produce small, high-quality features with minimal heat and high accuracy so they can keep pace with the fast-changing medical device market.
For more information about CMS Laser’s ultrafast picosecond and femtosecond laser drilling capabilities, visit our ultrafast lasers page.
0 comments
Leave a comment.